limitations of hardness testing|standards for hardness testing : ODM Hardness testing does have some limitations and challenges that can affect the accuracy and repeatability of hardness results, some of which are listed below: It is necessary to have properly prepared the surface of the sample to . What is the autoclave temperature range? Autoclave commonly runs at temperatures between 250° F (121° C), 270°F (132°C), to 275°F (135° C). [2] It’s essential to expose the items being sterilized at this temperature for a certain .
{plog:ftitle_list}
$18.25
Hardness testing does have some limitations and challenges that can affect the accuracy and repeatability of hardness results, some of which are listed below: It is necessary to have properly prepared the surface of the . In this article, we briefly explained the importance and application, advantages and disadvantages of Rockwell hardness test. We also introduce the Rockwell test with different .
Hardness testing does have some limitations and challenges that can affect the accuracy and repeatability of hardness results, some of which are listed below: It is necessary to have properly prepared the surface of the sample to .
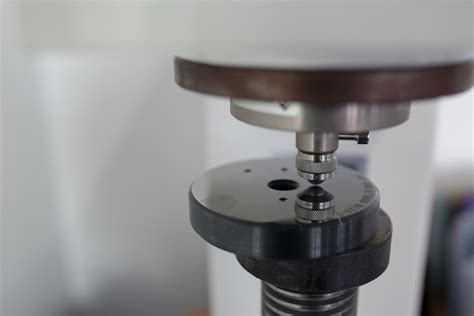
In this article, we briefly explained the importance and application, advantages and disadvantages of Rockwell hardness test. We also introduce the Rockwell test with different indenter types, such as diamond cones and carbide balls.1. Introduction to Hardness Testing. Hardness has a variety of meanings. To the metals industry, it may be thought of as resistance to permanent deformation. To the metallurgist, it means resistance to penetration. To the lubrication engineer, it means resis-tance to wear. To the design engineer, it is a measure of flow stress.
The Rockwell method has the following disadvantages: It is not always the most accurate hardness testing method, as even a small differential depth measurement error can lead to a significant error in the calculated hardness value.What is the Rockwell Hardness Test? Rockwell Hardness Test Procedure: A Step-by-Step Guide. How Does the Rockwell Hardness Test Work? How to Use a Rockwell Hardness Tester? Interpreting the Results with a Rockwell Hardness Test Chart. How to Calibrate a Rockwell Hardness Tester. What is the Standard for the Rockwell Hardness Test?
what is hardness testing
Hardness testing assesses a material’s ability to resist permanent deformation at its surface by applying pressure with a harder material. It finds applications across various industries for comparing and selecting materials, as well as ensuring quality control in manufacturing or hardening processes.

This article describes the principal methods for macroindentation hardness testing by the Brinell, Vickers, and Rockwell methods. For each method, the test types and indenters, scale limitations, testing machines, calibration, indenter selection and geometry, load selection and impression size, testing methodology, and testing of specific . Hardness testing is a vital process in many industries. Our guide explains everything you need to know about this crucial technique. From testing methods to the key applications, we cover it all to help you stay informed.
Hardness test methods in the macro range include Brinell, Vickers and Rockwell. Hardness testing in the low-load range applies when the test load falls between an interval of 0.2 kgf and 5 kgf (test load ≥ 0.2 kgf and < 5 kgf). The most commonly used low-load method is Vickers.
The advantage of Rockwell hardness testing is the relatively short testing time and good automation capability, as the measured values are determined directly from the indentation depth without optical measurement under a microscope.
static hardness testing
Hardness testing does have some limitations and challenges that can affect the accuracy and repeatability of hardness results, some of which are listed below: It is necessary to have properly prepared the surface of the sample to .
In this article, we briefly explained the importance and application, advantages and disadvantages of Rockwell hardness test. We also introduce the Rockwell test with different indenter types, such as diamond cones and carbide balls.1. Introduction to Hardness Testing. Hardness has a variety of meanings. To the metals industry, it may be thought of as resistance to permanent deformation. To the metallurgist, it means resistance to penetration. To the lubrication engineer, it means resis-tance to wear. To the design engineer, it is a measure of flow stress.
The Rockwell method has the following disadvantages: It is not always the most accurate hardness testing method, as even a small differential depth measurement error can lead to a significant error in the calculated hardness value.What is the Rockwell Hardness Test? Rockwell Hardness Test Procedure: A Step-by-Step Guide. How Does the Rockwell Hardness Test Work? How to Use a Rockwell Hardness Tester? Interpreting the Results with a Rockwell Hardness Test Chart. How to Calibrate a Rockwell Hardness Tester. What is the Standard for the Rockwell Hardness Test?
Hardness testing assesses a material’s ability to resist permanent deformation at its surface by applying pressure with a harder material. It finds applications across various industries for comparing and selecting materials, as well as ensuring quality control in manufacturing or hardening processes.This article describes the principal methods for macroindentation hardness testing by the Brinell, Vickers, and Rockwell methods. For each method, the test types and indenters, scale limitations, testing machines, calibration, indenter selection and geometry, load selection and impression size, testing methodology, and testing of specific .
Hardness testing is a vital process in many industries. Our guide explains everything you need to know about this crucial technique. From testing methods to the key applications, we cover it all to help you stay informed.Hardness test methods in the macro range include Brinell, Vickers and Rockwell. Hardness testing in the low-load range applies when the test load falls between an interval of 0.2 kgf and 5 kgf (test load ≥ 0.2 kgf and < 5 kgf). The most commonly used low-load method is Vickers.
standards for hardness testing
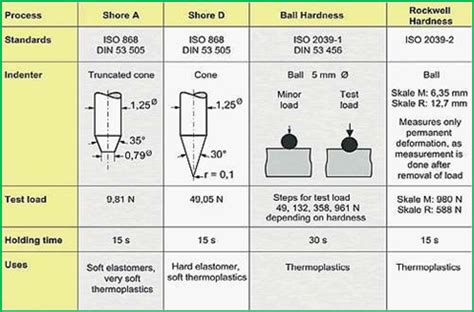
iso 8655 pipette calibration frequency
iso 8655 pipette specifications
When used properly, autoclaves are safe and highly effective. Autoclaves use saturated steam under pressure of approximately 15 pounds per square inch to achieve a .Fluctuations in temperature can lead to incomplete curing or defects, such as resin-rich or resin-poor areas, which may weaken the composite. Therefore, the temperature must be controlled carefully with .
limitations of hardness testing|standards for hardness testing